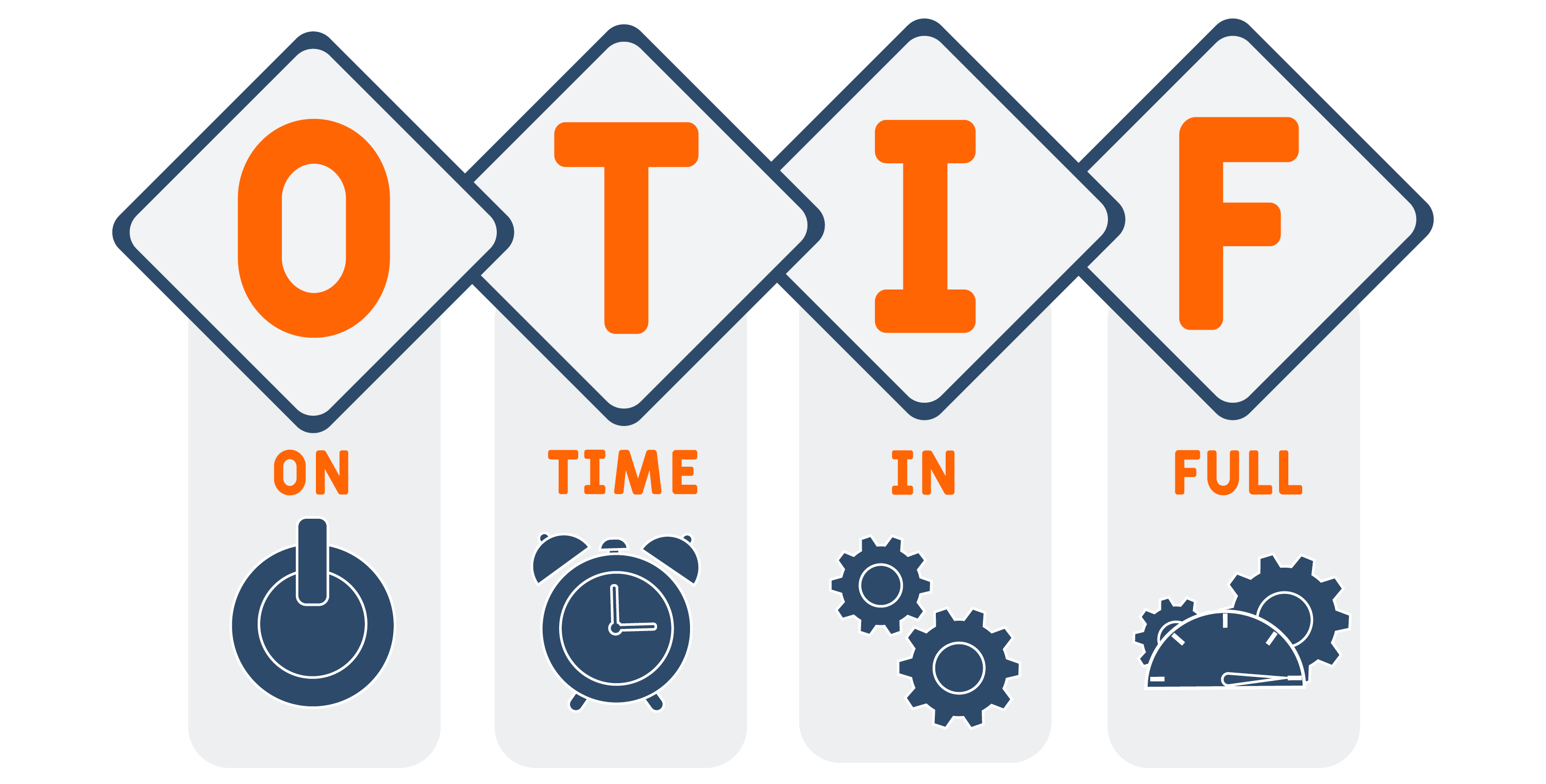
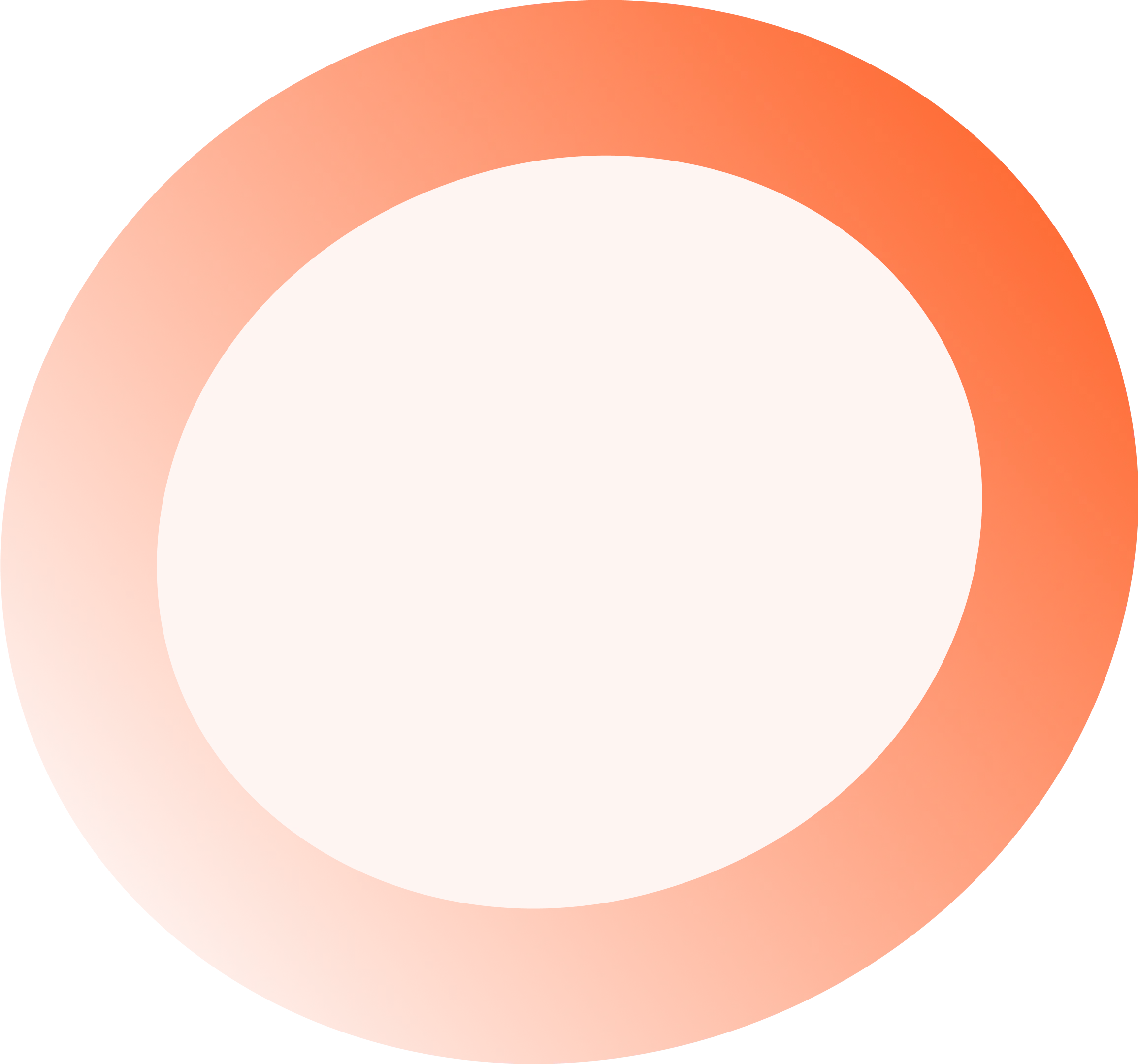
How to Ensure On-Time In Full (OTIF) Delivery of Your Manufacturing Orders
In the fast-paced world of manufacturing, delivering products On-Time In Full is not just a goal—it’s a necessity. In a world with increasing supplier options and improving SLA standards, customers value reliability more than ever. In such a case, late or incomplete deliveries can lead to lost revenue and even damaged customer relationships.
Let’s take a look into some actionable strategies that will help you ensure OTIF delivery.
What is OTIF, and Why Does It Matter?
On-Time In Full is a key performance indicator in the manufacturing industry and measures the percentage of orders with the promised quantity delivered within the promised timeline.
When you consistently deliver on time and in full, you enhance customer satisfaction, showcasing the reliability of your services. At the same time, this directly translates to enhanced efficiency in your operations. It also directly impacts your profitability as late or incomplete deliveries can lead to penalties, higher logistics costs, or lost sales. In an industry where tight margins and high expectations go hand-in-hand, mastering OTIF sets you apart as a dependable supply partner.
5 Key Reasons for Missed OTIF Targets
Even though accomplishing OTIF deliveries is all a manufacturer worries about, the goal comes with its own set of complexities. Here are some common challenges you are likely to face when striving for OTIF deliveries.
- Supply Chain Disruptions
Raw material shortages, unreliable suppliers, and transportation delays have the potential to throw off your entire production schedule. Global supply chain uncertainties such as weather disruptions or geopolitical issues can further complicate a timely procurement.
- Production Bottlenecks
Inefficiencies in production, such as machine breakdowns, poor scheduling, or workforce shortages, are known to slow down manufacturing. If one stage in production is delayed, the complete supply chain can be adversely affected.
- Demand Volatility
Fluctuating customer demand makes it difficult to balance inventory levels with production capacity. Underestimating client demands can lead to stockouts and late deliveries. On the other hand, overestimating demands results in excess inventory, which raises storage costs.
- Quality Issues
Defective products, rework, and quality control failures can cause delays in shipment and customer returns, leading to missed OTIF targets. Poor product quality not only affects delivery timelines but also damages your reputation while increasing project costs.
- Lack of Transparency in Supply Chain
Poor communication within your supply chain makes it difficult to track progress and identify bottlenecks. The lack of a clear picture of the process can also hinder the issue resolution part of the process, delaying deliveries further. Without real-time data, issues may go unnoticed until they cause significant disruptions.
Top 5 Actionable Strategies to Ensure OTIF Delivery
From optimizing your supply chain to harnessing advanced technologies, here are some results-driven steps to help you consistently meet your delivery commitments.
1. Optimize Your Supply Chain
Supplier Collaboration: Use systems like Vendor-Managed Inventory (VMI) or Just-in-Time (JIT) inventory management for clear communication as well as timely raw material delivery.
Supplier Diversification: Avoid reliance on a single supplier to reduce risks. Instead, try to onboard alternative suppliers as well to mitigate disruptions.
Demand Forecasting: Utilize historical data, market trends, and predictive analytics to plan production schedules effectively.
Smart Inventory Management: Maintain optimal stock levels to prevent shortages or excess inventory. You can also implement real-time inventory tracking for improved OTIF performance.
2. Streamline Production Processes
Lean Manufacturing: By adopting lean manufacturing practices like value stream mapping and 5S, you can significantly eliminate waste while reducing lead times.
Preventive Maintenance: Regular servicing, IoT sensors, and predictive tools play an important role in preventing breakdowns.
Advanced Scheduling: Advanced Planning & Scheduling software products provide ample support in optimizing production while keeping an eye on factors like capacity, labor, and priorities.
Quality Control: To ensure defect-free products, you can integrate Statistical Process Control and automated inspection systems within the production process.
3. Leverage Relevant Technology
Technology is a game-changer in achieving OTIF delivery, offering tools that enhance efficiency and visibility across operations.
Enterprise Resource Planning: ERP systems equip you with real-time insights across operations such as procurement, production, and delivery supporting you in better decision-making.
Manufacturing Execution Systems: When it comes to tracking production in real-time, MES enables you to identify delays and optimize workflows, ensuring schedules stay on track.
Robotic Process Automation: If you’re looking to improve accuracy in repetitive tasks, then RPA might be the best fitting solution. Not only does it automate repetitive tasks, it also reduces human error, and enhances precision for faster, consistent production.
Digital Twin Technology – Creates a virtual replica of the manufacturing process to simulate scenarios and detect potential issues before they cause disruptions.
4. Enhance Collaboration
Effective communication is crucial for achieving OTIF delivery, ensuring smooth collaboration across all areas of your operations.
Cross-Functional Teams: Introducing cross-functional teams that integrate procurement, production, logistics, sales, etc enhances communication throughout the process, maintaining alignment with end goals.
Real-Time Data Sharing: Cloud-based platforms provide up-to-date information, improving transparency and decision-making, hence are a reliable for real time data sharing.
Customer Collaboration: By closely collaborating with the customers, you can understand their needs in depth, share timely updates, and improve customer satisfaction.
5. Monitor and Measure Performance
To drive continuous improvement in OTIF performance, it’s essential to monitor and measure key metrics regularly. KPIs or dashboards are valuable tools for tracking performance indicators such as OTIF rate, production cycle time, order accuracy, etc.
When delays or incomplete deliveries happen, root cause analysis becomes crucial as it pinpoints the underlying issues, enabling you to take corrective actions. Additionally, conducting regular reviews with your team ensures that progress is evaluated, and challenges are addressed as required. By maintaining a focus on measurement, you can consistently achieve higher OTIF performance.
Sevenloop – A Reliable Partner for OTIF Goals
Ensuring On-Time In-Full (OTIF) delivery is a multifaceted challenge, but with Sevenloop, manufacturers can turn this challenge into a competitive advantage. By leveraging our set of innovative tools, you can optimize your supply chain, streamline production processes, and improve communication. With Sevenloop’s cutting-edge technology, you can not only meet deadlines but also consistently deliver value to your customers, building a reputation for reliability in the process.
OTIF isn’t just about meeting commitments; it’s about exceeding customer expectations. With Sevenloop, you have the right strategies and tools at your fingertips to turn OTIF excellence into a key driver of your manufacturing success.