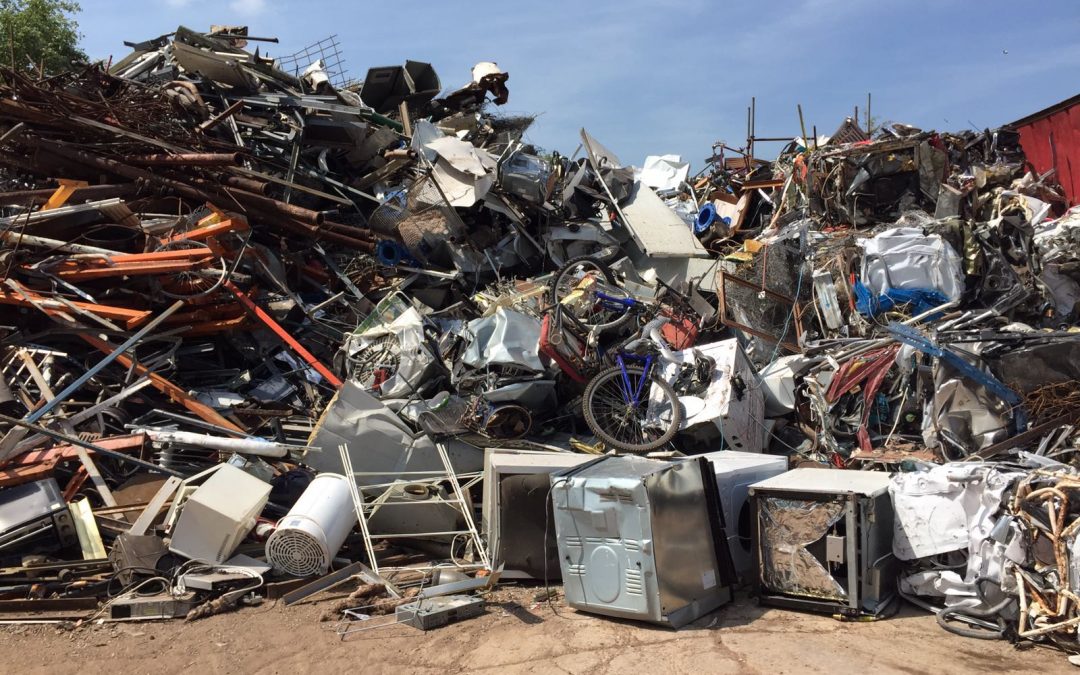
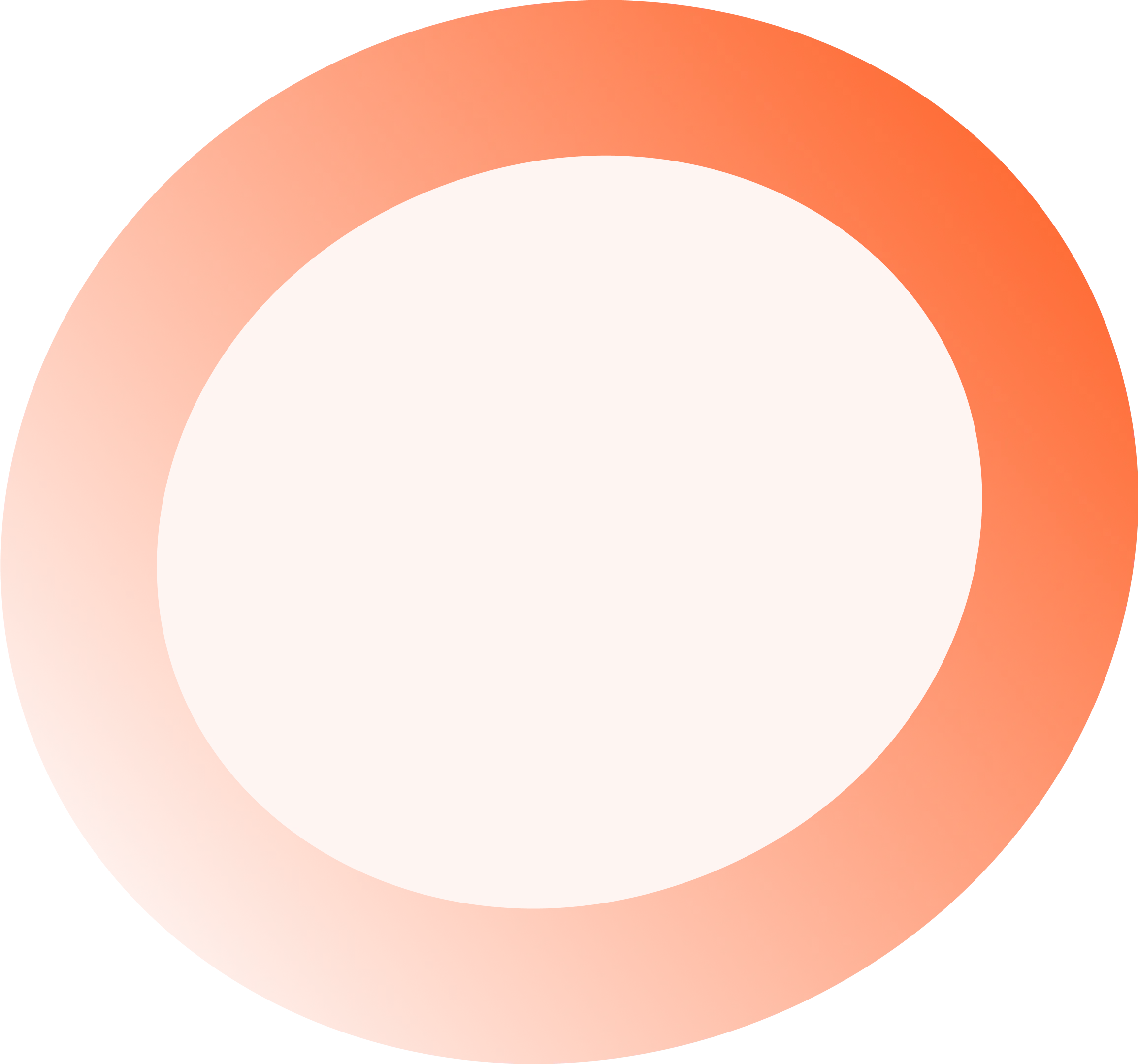
Recycling and Reusing Metals for Casting - Cost and Environmental Benefits
The casting industry relies heavily on metals and alloys as input materials for producing essential components across various sectors, from automotive to aerospace. Traditional casting production processes have often been criticized for their high costs as well as adverse environmental impact. In fact, each pound of casting produces approximately five to ten pounds of scrap waste in the form of flashings or sprue waste.
Recycling alloys for casting provides a sustainable alternative that offers not only economic benefits but also ecological advantages. Let’s look into some of the major benefits of adopting metal recycling in foundries.
6 Cost-Saving Benefits of Recycling Metals
The financial advantages of metal recycling are significant, reducing costs across the supply chain. Here are some aspects of financial sustainability for foundries that recycle their metal and alloy waste.
Reduced Raw Material Costs
Recycled alloys are generally less expensive than virgin materials. Producing metals like aluminum or steel from raw ores involves energy-intensive mining, refining, and smelting processes, all of which add to the cost. Recycling, by contrast, eliminates many of these steps, resulting in a much cheaper material. For example, recycling aluminum uses only about 5% of the energy required for its extraction from bauxite, drastically lowering production costs.
Lower Energy Consumption
Recycling alloys requires significantly less energy compared to extracting metals from their raw ores. In fact, recycling steel, one of the most common metals in the manufacturing industry, requires 56% less energy than producing it from iron ores. Lower energy usage directly translates to cost savings on electricity and fuel. For such an energy-intensive industry like castings, these savings can be reinvested into your business for upgrading equipment or expanding capacity.
Minimized Waste Disposal Costs
By reusing internal scraps, and remelting defective castings, you can significantly reduce the amount of waste. This not only lowers the costs associated with waste management, such as landfill fees but also eliminates the need to transport scrap to disposal sites. In some cases, scrap metal can even be sold to recycling facilities, turning waste into a source of revenue.
Improved Equipment Longevity
The use of recycled alloys often reduces the wear and tear on furnaces, molds, or other equipment. For instance, recycled alloys may require lower melting temperatures or involve fewer impurities. As a result, they tend to bring about smoother operations as well as less equipment degradation. This results in extended equipment life, reducing the need for costly repairs.
Mitigation of Commodity Price Volatility
Virgin metals are subject to fluctuating global market prices as they are influenced by factors such as geopolitical instability, supply chain disruptions, changing demand, etc. Recycled alloys insulate manufacturers from these price swings by providing a cost-effective, yet more predictable alternative. Such stability allows businesses to plan their budgets while avoiding unexpected increases in production costs.
Efficient Use of Internal Resources
Recycling and reusing alloys enable manufacturers to close the material loop within their operations. Instead of purchasing new materials for every production cycle, foundries can repurpose their own scrap by melting. This practice also reduces procurement costs.
Top 5 Environmental Advantages of Alloy Recycling
Recycling and reusing alloys offer significant environmental advantages by reducing resource extraction, energy consumption, and pollution. Some of the key benefits include:
Reduction in Resource Depletion
Recycling alloys reduces the need to extract raw materials like bauxite, iron ore, etc. As mining activities are resource-intensive, they often lead to habitat destruction, deforestation, soil erosion, and groundwater depletion. By reusing alloys, the casting industry plays a large role in conserving finite natural resources. Moreover, this practice also reduces the ecological footprint of mining operations on natural ecosystems.
Reduction in Air and Water Pollution
The recycling process produces fewer pollutants compared to primary metal production. Smelting ore releases significant amounts of harmful emissions accompanied by toxic byproducts into the atmosphere, including nearby water sources. Recycling minimizes these emissions while keeping air and water cleaner for the surrounding communities.
Lower Carbon Emissions
Recycling alloys significantly reduces the carbon footprint of metal production. Processes like mining, smelting, and refining of metals emit large amounts of greenhouse gases. For instance, recycling steel reduces carbon emissions by 58% compared to producing steel from iron ore. Similarly, recycling metals like aluminum or copper can significantly cut emissions depending on the type of metal. By adopting recycling, manufacturers directly contribute to meeting global emission reduction targets.
Waste Reduction and Landfill Diversion
Scrap metals and alloy waste that are not recycled often end up in landfills, increasing environmental pollution and taking up valuable space. Recycling alloys divert these materials from landfills, reducing environmental contamination caused by the leaching of heavy metals.
Support for a Circular Economy
Recycling or reusing alloys aligns with the principles of a circular economy, where resources are repurposed rather than discarded. This reduces the overall demand for virgin materials, promoting sustainable manufacturing practices.
The environmental benefits of alloy recycling extend beyond manufacturers to society at large, making it a win-win proposition for industry and the planet.
5 Technical Innovations That Make Alloy Recycling Easy
Technological advancements are revolutionizing how the casting industry recycles and reuses alloys. These innovations ensure higher efficiency and quality in the recycling process:
Advanced Sorting Techniques
One of the most significant advancements in alloy recycling is the use of advanced sorting technologies such as X-ray fluorescence (XRF) and laser-induced breakdown spectroscopy (LIBS). These systems allow foundries to analyze the chemical composition of scrap metals in real time, ensuring precise sorting as well as minimizing contamination. By accurately categorizing alloys based on their properties, these technologies help maintain the quality of recycled materials while reducing waste and operational inefficiencies.
Induction Furnaces
Modern induction furnaces are designed to handle mixed scrap efficiently with the help of integrated scrap management systems. These furnaces leverage sensors to automatically adjust the melting process according to the input material. With precise temperature control, these furnaces reduce energy consumption and preserve the integrity of recycled alloys. This ensures that foundries can produce high-quality alloys with consistent properties.
Automated Scrap Pre-Processing Units
Foundries are adopting automated scrap pre-processing units to prepare scrap metal before it enters the recycling process. Shredders, balers, and crushers are used to break down bulky scrap into smaller, manageable pieces while removing impurities like coatings, paint, non-metallic residues, etc. This pre-processing step not only improves furnace efficiency but also reduces recycling costs, resulting in a cost-effective operation.
High-Temperature Vacuum and Induction Melting
Technologies like vacuum induction melting (VIM) and vacuum arc remelting (VAR) have enhanced the ability to recycle alloys with high purity as well as controlled properties. These processes allow manufacturers to refine recycled alloys by melting in a controlled environment, eliminating impurities while ensuring consistent quality. For instance, the aerospace and defense sectors rely on these techniques to manufacture turbine blades and structural components from recycled superalloys.
Vacuum Degassing
To ensure the purity of recycled alloys, many foundries utilize vacuum degassing technology during the melting process. This technique removes gases such as hydrogen and nitrogen from the molten metal, enhancing the mechanical properties of the final product. By achieving high-purity recycled alloys, foundries can meet the stringent quality standards required for industries like automotive and aerospace.
Advanced Alloy Recycling With Sevenloop
Recycling and reusing alloys in the manufacturing industry not only delivers significant environmental benefits but also unlocks tremendous cost savings for businesses. By reducing reliance on raw material extraction and minimizing energy-intensive production processes, foundries can drastically lower their carbon footprint. The adoption of advanced recycling technologies ensures that high-performance alloys retain their quality, enabling industries to meet growing sustainability demands without compromising on performance or profitability.
At Sevenloop, we’re redefining how the manufacturing sector approaches metal and alloy recycling. With deep expertise in the recycled metal value chain, we enable access to low-cost, high-quality recycled alloys for manufacturers so that they are able to control their raw material costs while progressing toward sustainability goals. Partner with Sevenloop to reduce waste, improve resource efficiency, and lead the charge toward a sustainable future in manufacturing.
References
- ‘In fact, each pound of casting produces approximately five to ten pounds of scrap waste in the form of flashings or sprue waste.’
http://www.mntap.umn.edu/industries/facility/metalcast/resources/zincalloy
- ‘ In fact, recycling steel, one of the most common metals in the manufacturing industry, requires 56% less energy than producing it from iron ores.’
https://www.generalkinematics.com/blog/many-benefits-scrap-metal-recycling/
- For instance, recycling steel reduces carbon emissions by 58% compared to producing steel from iron ore.